18 Feb 2021
Sellafield DSA looks ahead to an even busier future
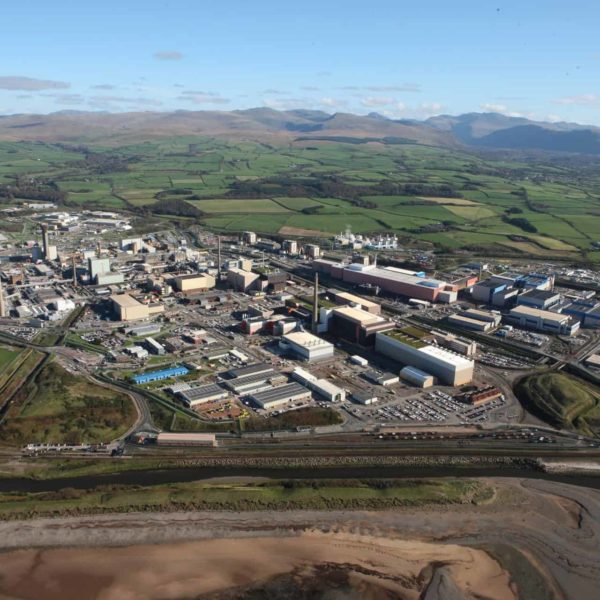
The Design Service Alliance (DSA) is an alliance between Sellafield Ltd, Cavendish Nuclear and major contractors in the nuclear supply chain to provide support to a wide range of decommissioning-related projects at the site.
Cavendish Nuclear leads the Progressive Alliance team which is delivering design, engineering and safety case services to Sellafield under the Design Services Alliance (DSA) framework.
Making a difference
The Design Services Alliance (DSA), launched nine years ago this month, can look back on many achievements. Currently active on more than 170 projects across the Sellafield site, it is also looking ahead to many more as it approaches its third five-year tranche.
There is a long list of ways in which the DSA makes a difference, for example by challenging engineering scope and making procurement smarter, or by applying lean techniques and better ways of working.
On the Cavendish Nuclear-led Sellafield Product and Residue Store Retreatment Plant (SRP) project, the DSA brought in an external specialist to produce an intelligent LED lighting scheme, saving an estimated £3.6m in energy and maintenance costs.
In Special Nuclear Materials (SNM), a review of plans to upgrade the electrical distribution system identified ways to reduce spending by more than £13m.
Also in SNM, the first ever opening and repacking of plutonium cans was made possible by an integrated team from the DSA and Site Management Project Office (SMPrO), which designed the complex and painstaking process, including a sealed glovebox, a bespoke can-cutting tool and repackaging equipment.
SMPrO’s decision to entrust safety case review work to the DSA is expected to cut costs by £15.6m over the next 10 years.
The DSA was instrumental in the design and manufacturing of the In-pond Manipulator, a crucial piece of equipment in the Legacy Ponds waste retrieval programme.
In collaboration with High Level Waste Plants, engineers successfully restored throughput in the vitrification plant by unblocking one of the calciners. They also introduced a new coupling design which dramatically reduced downtime.
One of most powerful aspects of the DSA approach is integrated design teams. This usually means a lower headcount and improved delivery to schedule. On SRP, integration meant that the team needed five fewer people for 34 months, cutting costs by £1.46m.
Collaboration with sub-contractors enabled the DSA to manage the removal of Sellafield’s greatest asbestos hazard, Development Centre B & P, which had to be stripped down to its steel frame.
The ability of DSA partner companies to provide a pool of skilled people with tacit knowledge enables the Plant Facing Design Office to both keep up with routine work and respond to plant breakdowns as quickly as possible with fit-for-purpose design solutions.
The DSA is not resting on its laurels. Initiatives are under way to reduce non-value adding work and enable engineers to spend more time on design delivery; and to increase engagement with manufacturers and installers so that designs are more outcome-focused, constructable, maintainable and manufacturable.